Innovations within air cargo
Measuring weight and volume
The air cargo industry is fast-paced and demanding, and personnel often face heavy physical labor, time pressure and safety hazards. However, innovations such as Weigh in Motion technology have not only improved operational efficiency, but also significantly reduced the workload for employees. In addition, dimensioning, in collaboration with one of our partners, enables real-time measurement of both the weight and volume of freight, providing even greater accuracy and safety on the work floor.
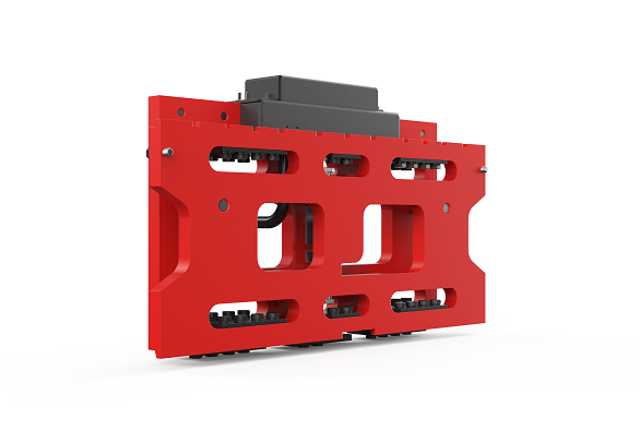
Safer work environment
Fewer movements and better distribution of cargo
Although pallets are not weighed manually, the traditional process of continuously driving back and forth to fixed floor scales involves unnecessary movements. This not only increases the risk of accidents, but also creates inefficiencies in the logistics process. Weigh in Motion technology eliminates the need for these extra trips by allowing pallets to be weighed directly during transport. This reduces the amount of movement on the shop floor, minimizes risk and contributes to a safer working environment for employees.
In addition to Weigh in Motion technology, sizing plays an important role in improving workplace safety within the air cargo industry. By measuring not only the weight but also the volume of pallets in real time, improper loads and overloading can be prevented. This ensures that cargo is better distributed and correctly stacked, significantly reducing the risk of accidents. In addition, dimensioning helps make more efficient use of space, leading to safer transportation and a better working environment for personnel.
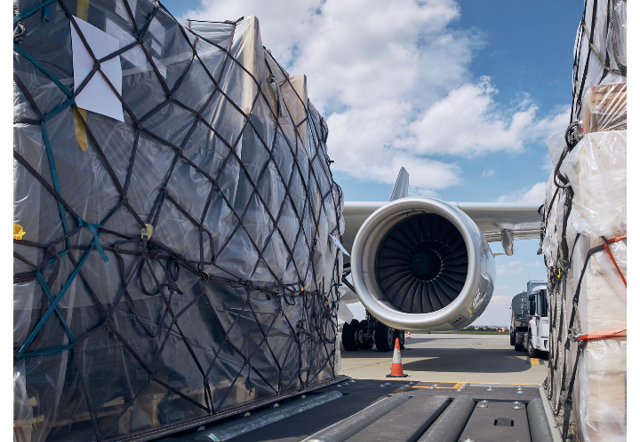
Bert de Greeff, Marketing & Product Manager at RAVAS
“RAVAS Weigh in Motion technology is ideally suited for moving large quantities of palletized goods within a short time frame.”
Less work pressure
More efficiency and less stress
In the hectic air cargo industry, time is often a crucial factor, and traditional weighing processes can cause delays in this regard. Driving back and forth to fixed weigh stations not only slows down operations, but also creates stress for employees who are under pressure to meet tight deadlines. With Weigh in Motion technology, pallets are weighed directly during transport, eliminating time-consuming intermediate steps. Dimensioning also makes it easy to optimally build large slave pallets. This streamlining of processes means employees can work faster and more efficiently, without the constant feeling of time pressure.
By reducing repetitive tasks and eliminating unnecessary movements, Weigh in Motion technology reduces the physical and mental strain on staff. Employees don't have to worry about incorrect weighing or delayed processes, leading to a lower error rate and a more productive work environment. Working more efficiently reduces stress levels and improves the team's overall work experience. In addition, employees feel less strained and more secure in their daily work, leading to higher job satisfaction.
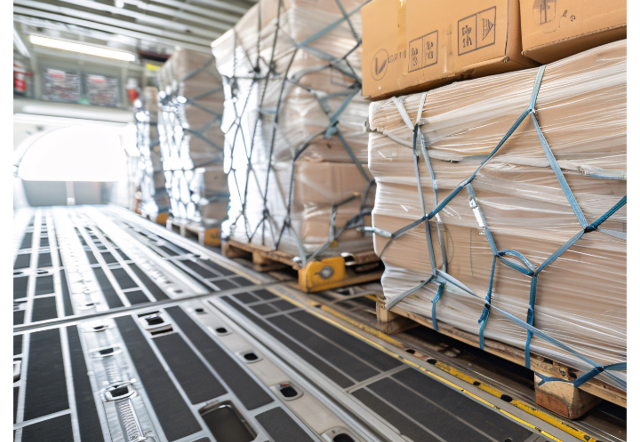
Want to know more? Download our in-depth white paper for free and discover how weighing data is transforming air cargo.