-
- Casos de éxito
-
ASTRA SWEETS REALIZA AHORROS DE COSTES INMEDIATOS CON EL PESAJE MÓVIL
Debido a una serie de variables inherentes a la producción de caramelos, Astra Sweets no sabía el peso exacto de las series de producción que salían por las tres líneas de colada. Las discrepancias en las existencias de productos semiacabados causaban material sobrante, retrasos en entregas y ciclos de producción adicionales correctivos. Ahora los sistemas de pesaje móviles RAVAS han sido instalados en los camiones que transportan los dulces desde las líneas al almacén, y los pesos de producción precisos se comunican con el sistema ERP a través de la red inalámbrica de la compañía.
Dulces de Turnhout
Merengues, gomas de vino, botellas de cola, gotas de regaliz, malvaviscos, menta: son todos los productos fabricados por Astra Sweets. En su planta principal de Turnhout, la compañía belga produce 300 tipos diferentes de dulces. Toda esta confitería es distribuia bajo su propia marca a supermercados, farmacias, gasolineras y mayoristas, o bajo marca propia a una gama de clientes importantes en Bélgica y en el extranjero.
En un recorrido por la planta de producción de Astra Sweets, se ven dulces pintados de colores vivos que salen de las máquinas, interminables bandejas de dulces siendo apiladas por robots, y camiones que conducen el caramelo al almacén de espera. Patrick Peeters, Producción de Usuario Clave, explica cómo funcionan las cosas: "Nuestros caramelos son vertidos en moldes de fundición de almidón. Dependiendo del tipo de dulces, el caramelo entonces va a una sala de secado, o a un almacenamiento frío. Después de 36 horas se aplica un acabado superficial, utilizando aceite, azúcar o ácido. El producto semiacabado entonces fluye a bandejas de 9 a 13 kg de caramelo cada una, que son apiladas sobre un palet y transportadas al almacén de espera. Luego de la aclimatación, los dulces son empaquetados según las órdenes de los clientes".
La producción y el empacado correctivos añadieron costes innecesarios
La gestión de existencias dejó espacio para mejoras, dice Stefan Verbeken, Gerente de Planificación y Suministro de Materiales de Astra Sweets. "Producimos en tres líneas de colada. Cada proceso de producción tiene sus pérdidas de arranque. Añada fallas durante una corrida y puede ver por qué la salida real puede diferir significativamente de la producción teórica esperada. Conocíamos la entrada de materias primas, por supuesto, pero no podíamos medir el rendimiento exacto al final de la línea. Por lo tanto, no podíamos estar seguros de cuánto de cualquier producto semiacabado había en existencia en el almacén de espera. Las discrepancias entre las existencias en nuestro ERP y las existencias en nuestro almacén podían ser de varias toneladas, dependiendo del tamaño de la producción".
Las incertidumbres en las existencias en espera producidas de productos semiacabados condujeron a ineficiencias y costes adicionales. Con el fin de mantener los cambios de productos en las líneas a un mínimo, todos los pedidos de los clientes, por ej: Las botellas de cola se agrupan en una sola línea de producción, se producen y luego se transportan al almacén de espera. "Si un producto semiacabado estaba planeado para múltiples pedidos de empaquetado, entonces esto estaba basado en el rendimiento teórico, con el riesgo de que para algunos pedidos se empaquetaba demasiado y para otros muy poco. Esto causaba cambios de última hora en la planificación de la producción para evitar problemas de entrega. Los cambios adicionales en las ejecuciones de empaquetado y las pequeñas ejecuciones correctivas de colada añadían costes innecesarios. En un punto, comenzamos a hacer inventarios diarios en el almacén de espera para evitar esto, gastando un montón de horas-hombre”.

"En un punto comenzamos a hacer inventarios diarios para contrarrestar el problema. Eso nos costó mano de obra que podríamos haber aprovechado en otro lugar. Utilizando las básculas móviles de RAVAS ahora generamos cifras reales, y podemos manejarlas en KPI's. Esto logró un ahorro inmediato de los costes, la inversión en los sistemas de pesaje se recuperó en un tiempo corto".
- Stefan Verbeken, Gerente de Planificación y Suministro de Materiales, Astra Sweets
La clave para la mejora: pesaje móvil
Se inició un proyecto de mejora: todo dulce que saliera de las líneas iba a ser pesado. Se consideraron diferentes opciones: la integración de los sistemas de pesaje en las líneas de producción resultaba costesa, pesar sobre una báscula de piso consumía mucho tiempo y posiblemente era insegura debido a los embotellamientos logísticos en el tráfico de almacén. Patrick Peeters había tenido experiencia con RAVAS en un antiguo empleador y propuso el pesaje móvil, en los camiones de almacén que realizaban el transporte de las líneas de producción al almacén de espera. Stefan Verbeken: "Resultó ser la solución más eficiente, así como también la más rentable".
Se presentó una solicitud de inversión, justificada por un análisis coste/beneficio. "Los cuatro sistemas de pesaje nos costaron aproximadamente 16.000 euros, pero también tuvimos que reemplazar dos camiones Yale más viejos, ya que habría sido un desperdicio de capital el construir una báscula en camiones a los cuales les quedan sólo unos pocos años en su ciclo de vida. Añadan 3.000 euros para los ajustes de Objective, el software que gestiona nuestras líneas de producción, y terminamos con 55.000 euros como inversión inicial. Los beneficios superaron fácilmente los costes. En los inventarios diarios y las correcciones de empaque ahorramos inmediatamente medio FTE. Añádase a eso: el empacado en el orden correcto, menos material de reposo y menos series correctivas. La aprobación llegó y Patrick Peeters se puso a trabajar con IT y otros departamentos involucrados".
Patrick Peeters describe el proceso de producción resultante: "Ahora tenemos cuatro camiones con báscula de pesaje. Tanto la báscula como el ordenador portátil en el camión se comunican con Objective a través de nuestra red WLAN. Una vez que el producto semiacabado sale de la línea, es pesado de inmediato. El operador inicia el protocolo en su ordenador portátil: ingresa el número de la línea de producción y la referencia del artículo, y luego activa a Objective para interrogar a la báscula acerca del peso. Eso completa el conjunto de datos. Desde el ordenador portátil se imprime una etiqueta de código de barras y el palet es transportado al almacén regulador".
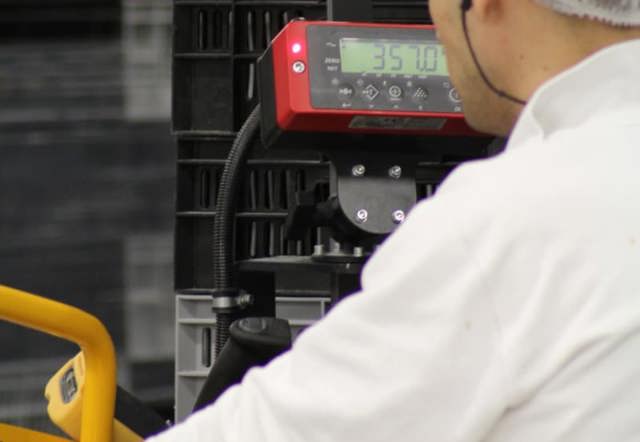
Dulces beneficios
"En dos de las tres líneas de producción se ha completado la integración de los sistemas de pesaje móviles con Objective, la tercera línea pronto será la próxima", dice Patrick. "Lo bueno de esto es que podemos comparar las líneas y ver los resultados de los sistemas de pesaje: en las dos líneas integradas ahora sólo quedan 50 kg de corrección por mes, lo que es una cantidad extremadamente pequeña en comparación con nuestro tonelaje mensual. En la tercera línea aún hacemos seguimiento y correcciones diarias. Si no lo hiciéramos, tendríamos diferencias de hasta 10 toneladas mensualmente. RAVAS nos está ayudando a limitar las correcciones diarias a un mínimo".
Stefan Verbeken: "Desde Objective los datos se importan al SAP. Ahora tenemos cifras reales luego del acabado, podemos hacer análisis de rendimiento por producto y a partir de allí optimizar. Podemos manejarnos por KPIs. La planificación de empaques se puede ajustar a las necesidades del cliente. Con los sistemas de pesaje móviles RAVAS hemos dado un paso adelante en nuestro proceso de producción".
COMPANY
Astra Sweets
LOCATION
Turnhout, Belgium
APPLICATION
Control de inventario
Control de inventario
Con las cadenas mundiales de suministro que operan a través de los continentes, con inventarios pequeños y entregas justo a tiempo, las empresas se han vuelto muy vulnerables a la escasez de los productos en inventario. La escasez implica procesos de producción interrumpidos, retrasos y pérdida de confianza del cliente. Todo lo anterior conlleva un costo. Con una báscula móvil, conectada a su sistema ERP o WMS, los flujos de materiales pueden ser monitoreados cada vez que se mueven las mercancías: mercancías entrantes, mercancías dentro y fuera de la producción, mercancías salientes. Sin interrumpir el proceso, las básculas móviles le permiten controlar con precisión su stock, reducir los niveles de existencias y reducir los costos.