
-
- Customer stories
-
Astra Sweets immediately saves costs with weighing trucks
Candy manufacturer Astra Sweets previously did not know the exact weight per production run. This led to residues, delivery delays or expensive corrective runs.
Business case
Astra Sweets
At its main plant in Turnhout, the Belgian company produces 300 different kinds of sweets. All this confectionery is distributed under its own brand name to supermarkets, drug stores, petrol stations and wholesalers, or under private label to a range of major customers in Belgium and abroad. Anyone who is shown around the production department at Astra Sweets will see cheerfully coloured sweets rolling out of machines. The sweets are stacked in trays by robots and transported on pallets by trucks to the intermediate storage facility.
Patrick Peeters, Key User Production, explains: "Our candy is poured into starch moulds. Then it goes to a drying room or refrigeration. The finishing touches are applied after 36 hours. The semi-manufactured product then flows into trays. These go on a pallet to the intermediate warehouse, where, after acclimatisation, the sweets are finally packed according to customer order."
Current situation
Buffer stock management left room for improvement, says Stefan Verbeken, Manager Planning and Material Supply at Astra Sweets. “We produce on three casting lines. Every production process has its startup losses. Add failures during a run and you can see why real output can differ significantly from the expected, theoretical output. We knew the input of raw materials of course, but we couldn’t measure the exact yield at the end of the line. Therefore we couldn’t be sure how much of any semi-finished product was in stock at the buffer warehouse. The discrepancies between the stock in our ERP and the stock in our warehouse could run into several Tons, depending on the size of the production run.”
The uncertainties in produced buffer stocks of semi-finished product led to inefficiencies and extra cost. In order to keep product switches on the lines to a minimum, all customer orders for e.g. cola bottles are grouped in a single production run, produced and then transported to the buffer warehouse. “If a semi-finished product was planned for multiple packaging orders, then this was based on the theoretical yield, with the risk that for some orders too much and for others too little was packaged. This caused last minute changes in production planning to avoid delivery problems. Extra switches in packaging runs and small, corrective casting runs added unnecessary cost. At one point we started doing daily inventories in the buffer warehouse to avoid this, spending a lot of man-hours.”

Investment in hardware and software
Astra Sweets invested in four weighing systems with WiFi, two RCS Hy-Q on double fork stackers and two RPW EL on electric pallet trucks.
How does it work?
An improvement project was initiated: all candy coming off the production lines had to be weighed. Several options were considered: building weighing systems into the production lines proved expensive, weighing on a floor scale time-consuming and not always safe due to logistical bottlenecks in internal traffic. Patrick Peeters had experience with RAVAS at a previous employer and suggested mobile weighing on the warehouse trucks that take care of internal transport from the production lines to the intermediate warehouse. Stefan Verbeken: "It turned out to be the most efficient and cost-effective solution."
An investment request was initiated, with a cost and benefit analysis to back it up. The costs consisted of four weighing systems, but also the replacement of two older trucks, because, according to Astra Sweets, it would be capital destruction to build a weighing system into trucks that had only a few years of useful life left. Add to that a cost of modifications to Objective, the software program that controls the production lines. The benefits far outweighed that. Half an FTE could be saved immediately on daily warehouse checks and all kinds of corrections in packing. Add to that: packing on the right order, less residue and waste and fewer corrective casting runs.
Patrick Peeters describes the current process: "We now have four trucks with weighing systems. Both the weighing system and the handheld on the truck communicate via our WLAN network with Objective. When the semi-finished product comes off the production line, it is immediately weighed on the truck. The operator starts the protocol on his handheld: he enters the number of the production line and which article it concerns. He then triggers Objective to request the weight from the weighing system on the truck, and thus the data set is complete. From the handheld, a label with a barcode is printed and the pallet goes to the intermediate warehouse."
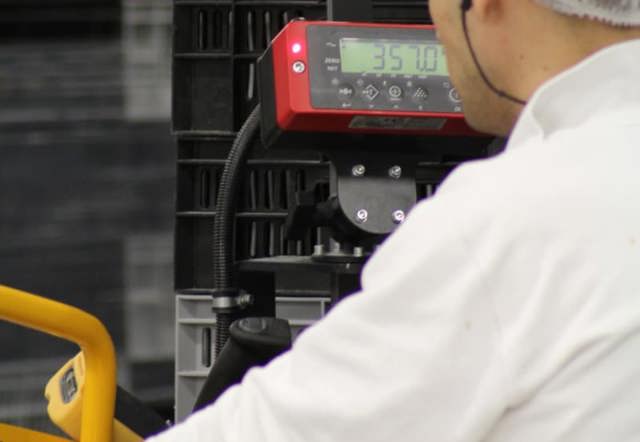
Stefan Verbeken, Manager Planning & Material Supply
“At one point we started doing daily inventories to counter the problem. That cost us manpower we could have used profitably elsewhere. Using the RAVAS mobile scales we now generate real figures, and can manage on KPI’s. This realized immediate cost savings, the investment in the weighing systems earned itself back in a short time.”
Results
Patrick Peeters: "The advantage of the integration between the weighing systems and Objective is that we can now compare the lines and see the results of the weighing systems. We only have 50 kg corrections on a monthly basis - which is extremely low compared to our monthly tonnage."
Stefan Verbeken: "The data goes from Objective to SAP. We now have real data after production. We can also do yield analyses per product and optimise from there. We can steer on KPIs. Packing planning can now be tuned much better to the needs of the customer. With the help of the RAVAS mobile weighing systems we have made a step forward in our production process."
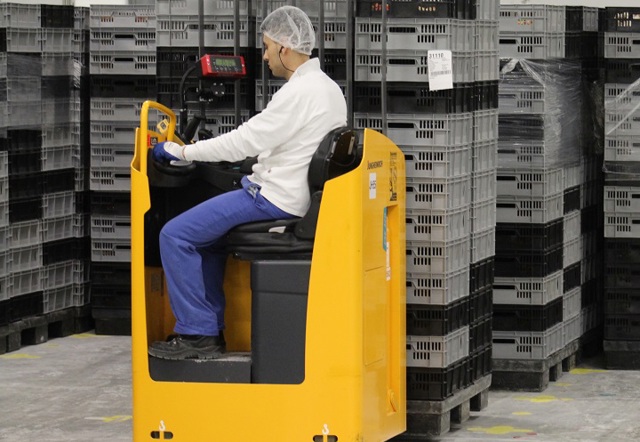
About the application
Stock control
With global supply chains that stretch across continents, with small stocks and just-in-time deliveries, companies have become very vulnerable to stock shortages. Shortages mean interrupted production processes, delays, loss of customer confidence. And they all come with a cost. With a mobile scale, connected to your ERP or WMS system, material flows can be monitored every time goods are moved: inbound goods, goods in and out of production, outbound goods. Without interrupting the process, mobile scales allow you to accurately control your stock, reduce stock levels and lower cost.