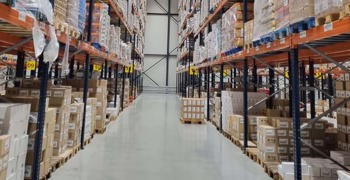
-
- Customer Stories
-
Van Rooijen saves time and resources with Pick by Weight
Van Rooijen Logistics uses the RAVAS' Pick by Weight to speed up their order-picking process and reduce errors. Dietsen Schrijvers, Account Manager at Van Rooijen Logistics, talks about his experiences collaborating with RAVAS.
Welcome to Van Rooijen Logistics. Van Rooijen is a family company that performs contract logistics for a broad client portfolio in the Benelux. Every day, they pick many order lines to be transported as outgoing pallets. To help them speed up their order-picking process and reduce errors, RAVAS implemented Pick by Weight.
Van Rooijen Logistics previously had to check each outgoing order for errors. With the RAVAS Pick by Weight solution, each unit is weighed to ensure accuracy. Also, since the data collected during the picking process is fully integrated into the WMS, operators receive an alert if an error occurs. As a result, manual tasks are eliminated, saving on personnel costs. It all happens in real-time and is 100% accurate.
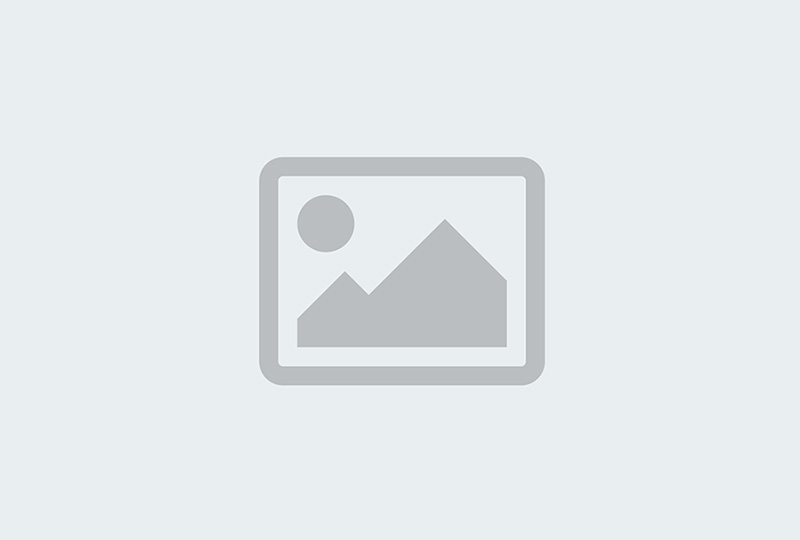
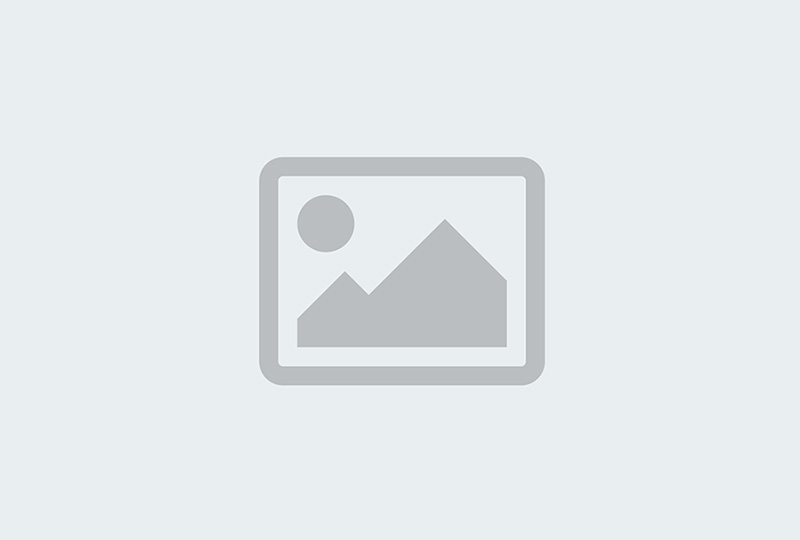
Dietsen Schrijvers, Accountmanager at Van Rooijen Logistics
“RAVAS makes work for Van Rooijen much easier and faster. The mobile weighing system is accurate and works very fast, so there is no time delay in the picking process.”
How does Pick By Weight work in practice
So how does Pick by Weight work? Consider this scenario: Kraft Heinz products are stored in Van Rooijen's warehouse, ready to be shipped to the end customer. In this example, an order is placed for 10 boxes of tomato ketchup, 10 boxes of tomato sauce, and 10 boxes of tomato paste.
Old situation
With their old process, a Van Rooijen employee logs in to his hand terminal, drives his order pick truck to the appropriate pick box, scans the item there, and picks the quantity displayed on his screen. When the entire order is complete, he moves the pick pallet to a check box and starts the next order. Someone else, meanwhile, checks the pick pallet. Unfortunately, one box of tomato paste was under-picked. The checker calls the picker in and asks him to get an extra package from the pick box. The extra time and required resources to correct the error cost time and money.
New situation
With mobile weighing technology, the Pick by Weight system knows the weight of each box. As a result, the order picker only has to scan the product ID and put boxes on the pallet; the weighing system knows when there are enough. Van Rooijen says: "We only have one person doing end checks of the orders now, where in the past we would have four." This improved process prevents errors and redundancies, thus saving time and money.
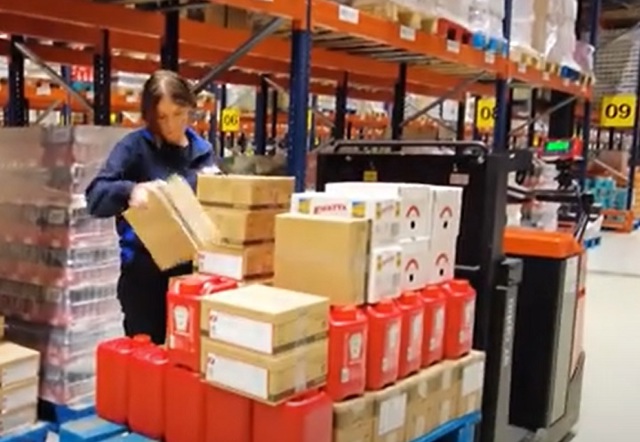
Dietsen Schrijvers, Accountmanager at Van Rooijen Logistics
“We only have one person doing end checks of the orders now, where in the past we would have four. This makes a big difference for us in terms of time and money.”
Three examples of Mobile Weighing Solutions
Learn how other companies are saving time, money and space by using innovative mobile weighing systems.
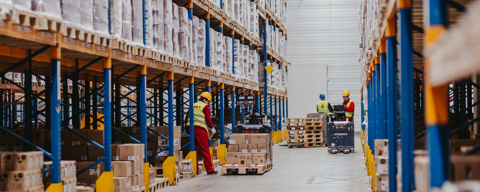
Raben: order picking with two weighing systems
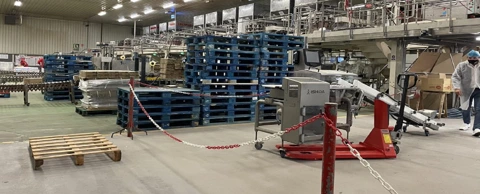
Frit Ravich prevents loss of raw materials
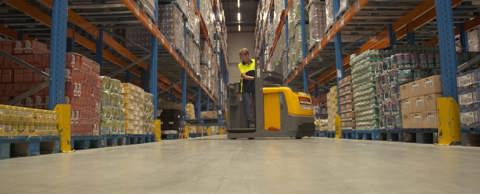
Kuehne+Nagel chooses Pick by Weight for supply chain optimization
Availability and compatibility
Sales partners
RAVAS works with worldwide sales partners. Here's a selection of OEM brands.
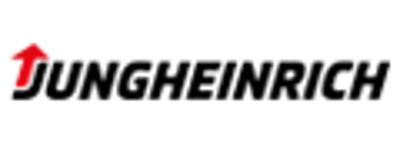
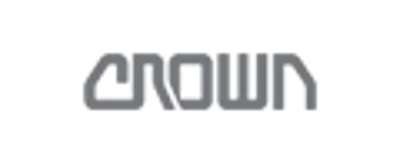
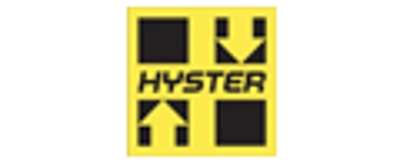
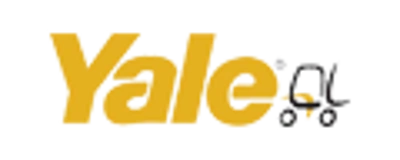
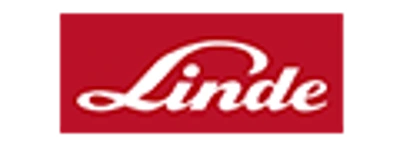
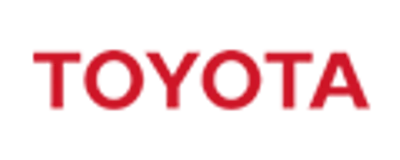
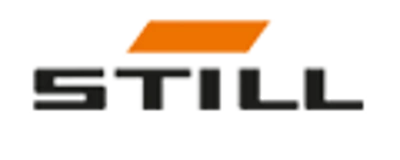
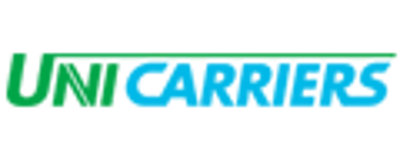